ARC WELDING IN INERT GAS WITH NON-CONSUMABLE TUNGSTEN ELECTRODES (T.I.G. Tungsten Inert Gas)
A. INTRODUCTION

Arc welding in an inert gas shield with a non-consumable tungsten electrode (T.I.G. – Tungsten Inert Gas or G.T.A.W. – Gas Tungsten Arc Welding) is a procedure in which the heat necessary to make the welding is supplied by an electric arc which is maintained between a non-consumable electrode and the workpiece. The electrode used to conduct the current is in tungsten or tungsten alloy. The welding zone, the melted metal and the non-consumable electrode are weatherproof thanks to the inert gas which is supplied by the electrode holder torch.
The TIG welding procedure can be used with the addition of external weld material (welding rod) or by melting the base material by means of the heat effect produced by the electric arc.
B. THE WELDING CIRCUIT

The welding circuit consists essentially of the following elements:
1.generatore di corrente
2. tungsten electrode-holder torch with cable bundle
3. welding rod
4. gas cylinder with pressure circuit
5. clamp with earth cable
6. water cooling unit
1. Power sourceThe purpose of the power source is to power the electric arc created between the base material and the tungsten electrode, through the output of current sufficient to keep the arc struck. Inside the power source there is usually a welding current adjustment device, of a mechanical (magnetic shunt) or electronic type (thyristor or inverter system).
It is possible to distinguish two categories of power source:


a) alternating current (AC) power source
The output current/voltage from the power source takes the typical form of a square wave, which changes its polarity at regular intervals with a frequency of 20 up to 200 cycles per second (Herz) or more, depending on the type of power source used. This is achieved by means of one or two devices whose function is to transform the current/voltage sine wave from the distribution network into a suitable alternating welding current/voltage.
b) direct current (DC) power source
The output current from the power source has a continuous wave form, which is obtained by means of devices that are able to convert the current/voltage from alternating to direct.
If the welding circuit consists of a direct current power source (DC), it can be further classified according to the method of connecting the power source poles to the material to be welded or the form of the welding current:
i) direct current with straight polarity connection
With staright polarity connection, the torch and its cable is connected to the negative pole and the material to be welded to the positive pole of the power source; in this case the electrons flow from the electrode towards the piece, causing melting.
This is the most frequently used type of current with the TIG system and it ensures good weldability for almost all commonly weldable metals and alloys, with the exception of aluminium. Direct current with straight polarity produces a narrow, deep weld pool and also a penetration that is decidedly better than that obtainable with reverse polarity.

ii) direct current with reverse polarity connection
When welding with this polarity the torch with its cable is connected to the positive pole and the piece to the negative pole of the power source.
This type of power supply is rarely used because it produces a flat weld pool with poor penetration. Reverse polarity in itself causes excessive heating of the electrode, and to prevent the electrode from burning, rather low current intensities should be used. This is the reason for its limited use.
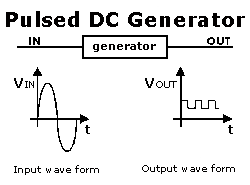
There is a further family of power sources, identified as direct current power sources irrespective of the polarity of the connection and named as modulated or pulsed direct current power sources.
The modulated current power source is a direct current power source fitted with particular devices used to vary the size of the welding current. Modulated or pulsed current is obtained by the superimposition on the direct base current of a further component, usually a square wave form, to produce a periodic pulsation of the arc.With this system a weld seam is obtained consisting of a continuous superimposition of spot welds that consecutively form a single seam. This method is typical of welds on thin materials where it is necessary to control the amount of heat so as to prevent the piece being perforated without diminishing the penetrability of the weld.
2. Tungsten electrode-holder torch with cable bundleThe electrode holder torch is a tool that encloses the tungsten electrode and is connected to a set of cables that are in turn connected to the power source and whose purpose is to supply electrical power and convey the gas shield.
Depending on the type of use, torches may be naturally cooled via the gas shield, if low current intensities are required, or water-cooled when high currents (200 – 500 A) and frequent welds are required.
3. Welding rod
The thickness of the material, the type of joint and the desired welding properties will affect the decision whether or not to use a metal welding material to add to the weld pool. The addition of metal welding material in manual welding is achieved by immersing a rod of the material in the arc zone, at the side of the weld pool.
The metal used is often similar to the base material metal and often includes a limited quantity of deoxidant additives or other elements to improve the properties of the melted area.
4. Gas cylinder with pressure circuit
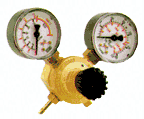
The gas cylinder with pressure circuit consists of:
– a cylinder containing the protective gas/es;
– a pressure gauge, used to indicate the quantity of gas in the cylinder;
– a gas regulator
– a solenoid valve, present if the torch is fitted with a pushbutton and controlled by this button, which opens and closes the gas flow according to the operator’s needs.
5. Clamp with earth cable
The clamp with the earth cable is used to make the electrical connection between the power source and the base material. The section and length of the cable will depend on the maximum current (amperes) of the welding power source.
6. Water cooling unitThe water cooling unit is a device used to cool the torch, if water-cooled, to prevent excessive overheating if high welding currents are present. By means of a pump, this apparatus gives continuous water circulation within the torch and controls overheating by means of a cooling system.
C. THE PROTECTIVE GASES
The main purpose of the protective gas shield is to replace the air near the weld pool, the electrode. The physical and chemical properties of the gas shield can have different effects on the weld depending on the various types of metal. The gases used for the shield in TIG welding are argon, helium, argon-helium or argon-hydrogen mixtures.
It is always important that these gases are as pure as possible since even insignificant percentages of impurities can influence the quality of the weld and make it unacceptable.
During welding using an argon gas shield, the arc is quite stable but the pool is cooler so that this gas is more suitable for welding thin material.
Argon is a widely used gas because it costs much less than helium; this is the main selection factor when chosing the shielding gas.
The arc with a helium shield generates more heat than that with argon; its use is therefore recommended for materials with high thermal conductivity, thus allowing an increase in the welding rate.
Since helium is lighter than air, to give the weld pool sufficient protection it must be used in greater quantities than those for argon.
Argon and helium mixtures are used to obtain gas shields with intermediate properties.
D. NON-CONSUMABLE ELECTRODES
There are various types of non-consumable electrodes on the market:
-
- pure tungsten electrodes. These are used with low current intensities and alternating current since the arc is more stable. In terms of cost, these are the cheapest electrodes.
-
- thorium-tungsten electrodes. These withstand high current intensities. The arc is easy to strike and, once struck, remains quite stable. These electrodes are recommended for welding steel with direct current and straight polarity.
-
- zirconium-tungsten electrodes. These are used for manual welding of aluminium, magnesium and its alloys, with a medium-low current intensity.
-
- cerium electrodes. These are distinguished by high electron emission and give good penetration with satisfactory resistance to wear.
E. ARC STRICKING SYSTEMS
– HF (high frequency) strike
The pilot spark is supplied by a high frequency generator that superimposes a high voltage impulse on the welding voltage; the power of this device is minimal, but at the same time sufficient to allow the electrical arc to be struck at a distance.
HF strikes require the use of a particular welding torch, which is fitted with a pushbutton used to control the strike.
– pilot arc strike
In this case the arc strikes between the tungsten electrode and an auxiliary electrode that may be a ring fitted to the nozzle of the torch itself.
The pilot arc is struck by a high frequency spark which intervenes in the actual pilot arc circuit; after the pilot arc has been struck, the pilot spark is disconnected since the principal pilot arc is struck spontaneously by a simple discharge of the tungsten electrode which becomes incandescent in the ionised gas atmosphere. The type of arc strike is used mainly in automatic units.
– LIFT strike
This is obtained by means of a device that supplies a small current (so as not to damage the tip of the tungsten electrode) when the electrode is in contact with the material to be welded.
When the electrode is taken away from the piece, a spark is created and this causes the arc to strike; the power source then increases the welding current until it reaches the preset value. Because high frequencies are not present, the LIFT strike does not create electromagnetic interference; however, the contact made by the tip of the electrode with the base material contaminates the weld pool.
– scratch strike
This strike is obtained by scratching the piece to be welded with the tungsten electrode, causing the arc to strike. The contact between the electrode and the piece to be welded causes tungsten inclusions in the start of the seam, which lowers the quality of the weld.
F. MATERIALS WELDED BY TIG
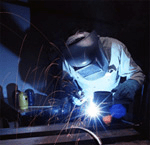
This procedure is mainly applied for welding stainless steel, aluminium and its alloys, nickel, copper, titanium and their alloys.
Stainless steel is welded in direct current (DC) with electrode negative polarity.
It is possible to weld thicknesses up to 2.5mm without adding weld material; thicker welds require bevelled edges and the use of the welding rod, the material of which should be particularly suitable for the stainless steel quality to be welded. Before proceeding to weld, thorough cleaning with a stainless steel brush is recommended.
Aluminium and its alloys should be welded with alternating current (AC) and, to achieve a good seam, they require the use of a suitably rated high frequency power source.
If there is high oxidation, it should be removed with a brush or by pickling (a chemical procedure for removing the oxidation).
It is also possible in this case to weld thicknesses up to 2.5mm without adding weld material; for thicker welds, the edges must be bevelled and the welding rod should be used.
Welding in an argon atmosphere using a tungsten electrode is also applied to mild steels and steel alloys, nickel and its alloys, copper and its alloys, titanium and noble metals. For all these metals and alloys direct current (DC) with straight polarity is used.